Revolutionizing Building Aesthetics with Modern EIFS Replacement Strategies
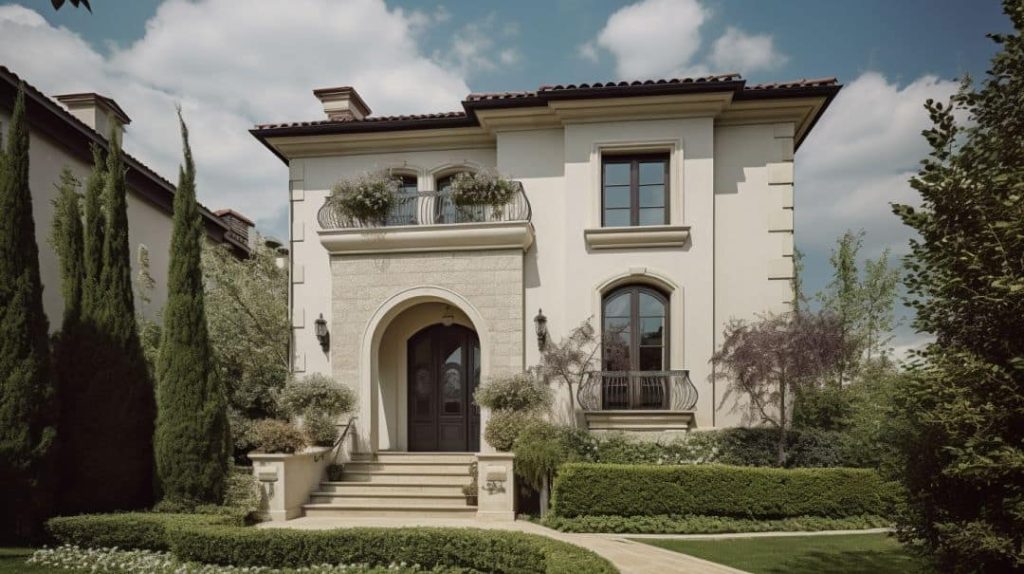
Introduction
Exterior Insulation and Finish Systems (EIFS) cladding arose in popularity in the 1980s and 1990s due to its energy efficiency and sleek, modern aesthetic. Also referred to as synthetic stucco, EIFS started out as an innovative construction technology developed to insulate interior spaces. However, as energy costs rose in the 1970s, EIFS emerged as an inexpensive way to wrap the exterior of homes and buildings with an insulated layer topped with colorful acrylic finishes.
But despite the initial EIFS craze driven by builders and homeowners, complaints soon emerged regarding water intrusion, persistent cracking issues, and faster than expected deterioration. Moisture penetration in particular has created extensive damage under the surface of many homes, requiring not just repairs but full removal and replacement of damaged EIFS components. Coupled with aesthetic constraints of EIFS’s plain, flat look, more and more property owners are exploring advanced techniques for replacing their problematic stucco siding for good.
This article will dive into common problems with EIFS constructions, quick-fix options, and how to determine when full replacement is preferable. We will also overview proper full EIFS removal methods and top replacement alternatives like fiber cement and traditional multi-layer stucco. By understanding current best practices for EIFS transformations, you can make the most informed decision on enhancing your home or building’s curb appeal, longevity and comfort.
Key Takeaways
Issue | Overview |
---|---|
Common EIFS Problems | Early EIFS is prone to moisture damage, cracking, detachment issues from flaws. |
Quick Fixes | Re-caulking, sealing cracks, patching holes. |
Replacement Deciding Factors | Major leaks/damage, desire for low-maintenance and durable alternative, improved aesthetics. |
Top Alternatives | Fiber cement, traditional 3-layer stucco systems. |
Understanding EIFS Siding
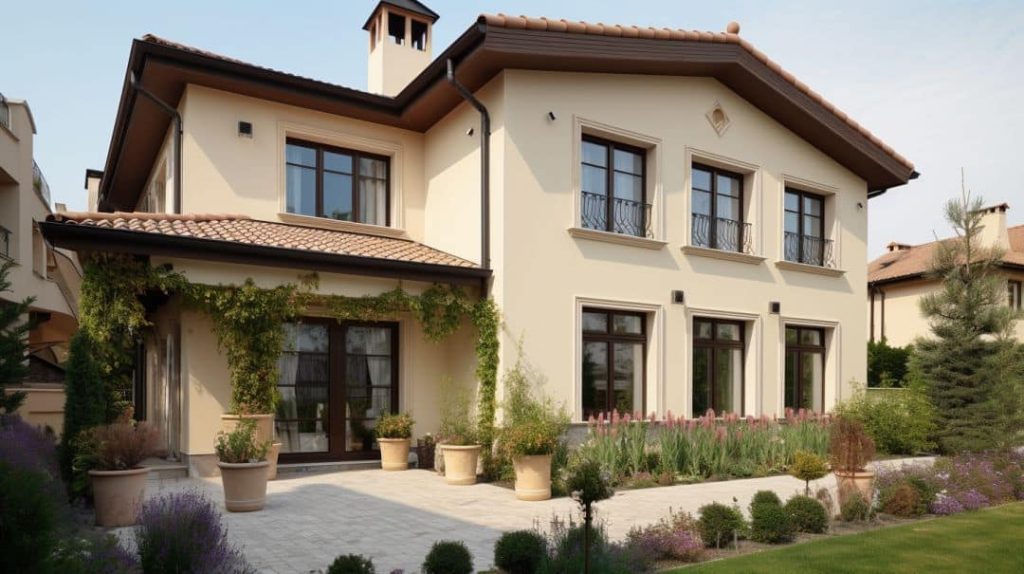
Brief History
EIFS stands for Exterior Insulation and Finish System. As a construction technology, it evolved in Germany in the 1950s and focused on interior thermal insulation needs. Europe’s temperate climate allowed EIFS to transition to enclosing building exteriors without immediately showing problems that would emerge across seasons in North America.
Seeing EIFS’s possibilities for boosting energy efficiency, builders and architects adopted the method in the US throughout the 1980s and early 1990s. It provided an inexpensive way to completely wrap existing home exteriors like brick, concrete, and plywood in continuous insulation up to 3 inches thick. This “retrofit” approach appealed to homeowners wanting to improve comfort without replacing entire walls or foundations.
However, as EIFS envelopes started to age, issues surfaced from the inherent moisture vulnerability and composition weaknesses in early formulations. Cracking, crumbling corners, sealant failures, and paint deterioration signaled that water was infiltrating the permeable layers causing underlying leaks, rot damage, and even mold growth inside walls. Without effective ways to fully examine behind facades, many issues went undetected for over a decade while gradually worsening conditions.
Quick Fixes for EIFS Cladding
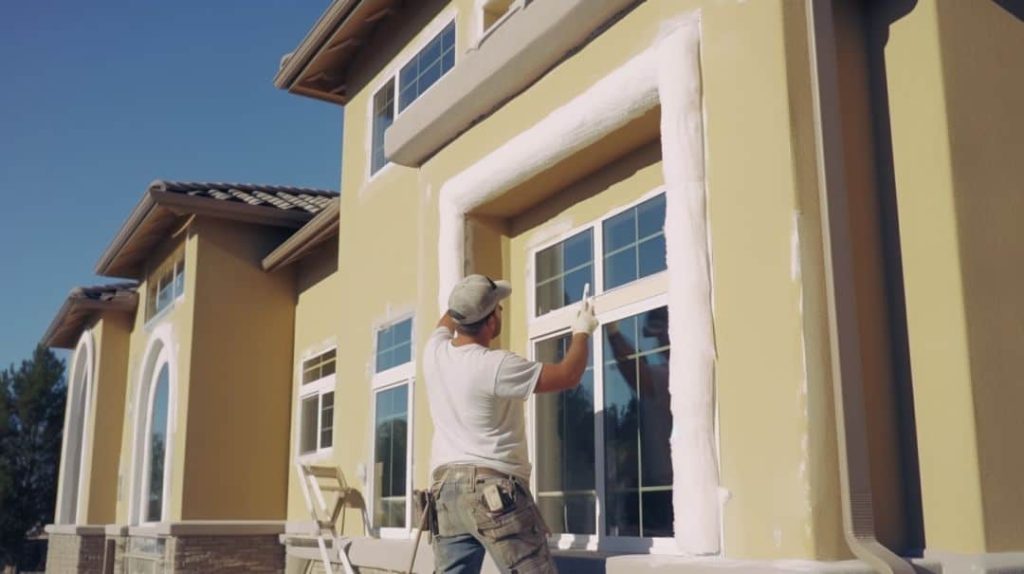
For less severe EIFS issues, homeowners may consider trying simple repairs first before considering full replacement. Quick fixes to extend the life of existing EIFS walls include:
Caulking & Re-Sealing
Examining all EIFS edges and joints and re-applying quality sealant can help prevent moisture entry through cracks and gaps. However, this is only a temporary solution if underlying insulation boards are misaligned or detachment exists.
Patching Holes & Indents
Small holes, dents, animal/pest damage, or holes from old fixtures can be patched with EIFS base coat material and retextured/painted. Larger holes may require cutting back insulation to remount flush with framing first.
Crack Injection Repairs
Specialty EIFS contractors can inject epoxy, polyurethane foam or grout into cracks to improve waterproofing and adhesion. However, large spiderweb cracking patterns point to more encompassing wall issues.
Recoating & Painting
Faded, flaking acrylic finishes can be rejuvenated by power washing, priming, and applying new integrated finish coatings. Thicker elastomeric textures better hide underlying cracks and defects.
Sealing All Flashing, Edges, Penetrations
Examining all intersections of EIFS with windows, roofing, decks, and other materials is key to preventing water entry. Fresh sealant, backer rod, drip edge flashing help protect vulnerable transition points if installed properly.
While cheaper in the short term, repainting and sealing existing EIFS kicks the can down the road if moisture or other problems lurk behind the surface. Quick fixes cannot reinforce overall structural integrity or longevity compared to proper system replacements.
As outlined in this recent article on EIFS sealants, even quality caulking and flashing repairs are temporary solutions.
Common Issues with EIFS
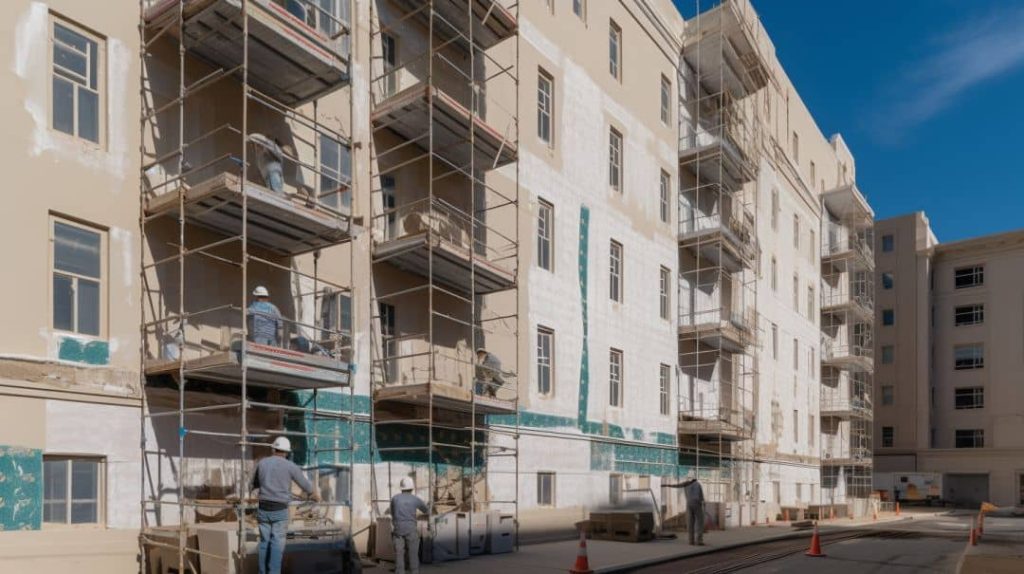
Understanding Underlying Damage
On the surface, cracking, chalking finishes, and water leaks may seem like simple fixes. However, the true root causes and encompassing damage are often invisible threats lurking underneath the outer EIFS skin.
Some hidden consequences homeowners may face over time:
- Rotting structural frames covered by permeable EIFS layers
- Sheathing decay & warping allowing even more water intrusion
- Mold & mildew accumulation degrading air quality and releasing toxins
- Pest intrusion exploiting gaps to infest walls, insulation
Catching and addressing EIFS failures early is crucial before water wreaks havoc on structural integrity. But pulling back finishes often reveals bigger issues than expected.
As we explored regarding hidden EIFS mold dangers, waiting on repairs makes problems exponentially worse. Whole wall reconstructions down to the studs are often needed – not just superficial fixes.
Parts of EIFS Prone to Failure
While the acrylic finishes tend to show issues first, defects are often tied to leaks from these vulnerable EIFS components:
- Joints Between Insulation Boards – Gaps allow water to seep behind finishes. Improper alignment also stresses seams.
- Window & Door Flashing – Poor integration during installation leads to leakage into openings and frames.
- Roof Line Intersections – Insufficient flashings, and shingling allow water migration behind finishes.
- Sealants & Expansion Joints – Early breakdown from weathering exposes zones for water entry. Cracking follows.
Like links in a chain, every EIFS layer and connection point impacts overall performance. Weakness in one component stresses the entire envelope system.
When to Consider EIFS Replacement
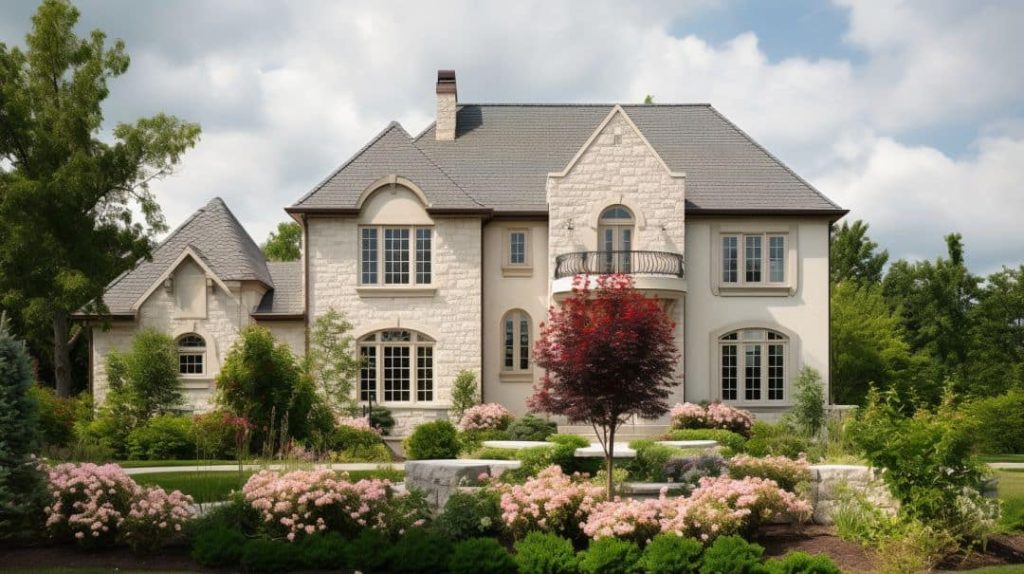
Extensive Water Damage
If leaks, floods, or other water intrusion events have saturated walls behind EIFS, removal and rebuilding may be required. Signs include:
- Large warped, dark areas showing excess moisture
- Detached areas or holes exposing blackened sheathing
- Peeling paint bubbling from trapped moisture
Even if underlying materials dry out, residual salts and corrosion accelerate system failures. Correcting water sources first then full enclosure replacement is advised.
Persistent Cracking Despite Repairs
No matter how much sealing and caulking, inherent flaws in the EIFS layers will lead to recurrent cracking at weak points. If fractures reappear quickly after repairs, moisture resistance is still lacking.
Desire for Durable, Low-Maintenance Alternative
After dealing with continual fixes, homeowners often want an easier, longer-lasting exterior solution. High-quality alternatives like fiber cement and conventional stucco require less upkeep over decades.
Improved Visual Appeal
For a more customized, attractive aesthetic, cladding options like cultured stone, smart siding, brick, and wood enable more personality. Removing restricting EIFS opens creative curb appeal possibilities.
The Best EIFS Alternatives
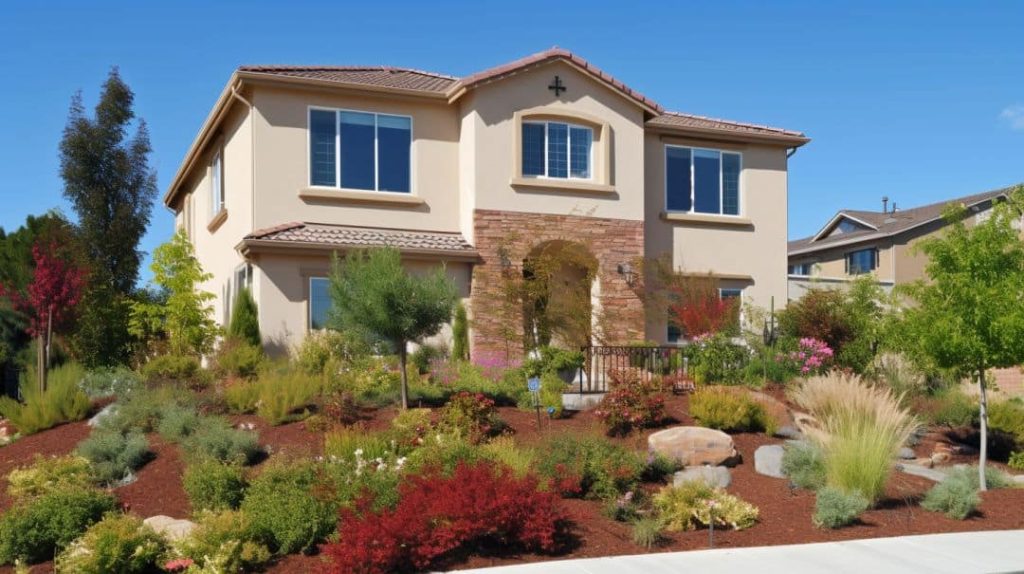
Fiber Cement
Fiber cement siding has gained popularity as a durable, aesthetically flexible replacement for aging EIFS walls. Benefits include:
- Longer lasting than real wood or vinyl (~50 years)
- Fire, impact, weather resistant
- Can be painted any color
- Won’t warp, crack like wood
- Provides continuous insulation options
Its dimensional shape and smooth/textured finishes enable more custom facades mimicking wood grain, stucco, etc. Fiber cement works well blended with existing brick or trim accents.
Traditional Multi-Layer Stucco
For homeowners wanting a similar stucco aesthetic without EIFS drawbacks, traditional 3-coat stucco is a proven solution.
- Standing the test of time across Europe for centuries
- Superior cracking resistance with reinforced scratch coat, brown coat layered above solid walls (not just foam)
- Effective moisture wicking using porous plaster top coats and drainage plane behind
- Thicker overall application (~7/8” vs 1⁄4” EIFS veneer)
With proper installation and maintenance, traditional stucco facades outlive EIFS constructions by decades, avoiding continual repairs. Blending color coats, textures and decorative finishes enable fully custom designs.
Why Choose EIFS Replacement
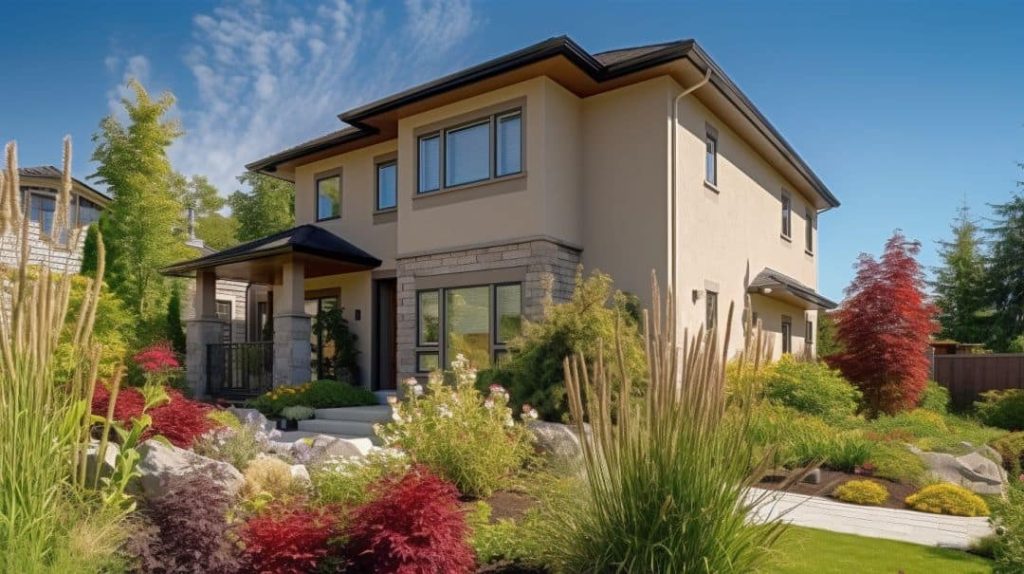
While no construction method is perfect, removing failing EIFS and replacing with an alternative system or materials can provide homeowners superior durability, design flexibility, and comfort for decades to come.
Many factors lead owners to decide replacement is worthwhile, such as:
- Eliminating recurring maintenance costs – Repainting, caulking EIFS every few years adds up fast, whereas fiber cement, stucco and other facades provide longer integrity.
- Improving moisture management – Advanced barrier designs and integration in new systems actively prevent water intrusion instead of trapping moisture.
- Increasing overall wall insulation – Code upgrades mean newer constructions better insulate and seal energy leaks for utility savings.
- Boosting aesthetic appeal – From diverse color choices to dimensional details, cladding variety offers curb appeal uniqueness, not flat ambiguous boxes.
- Adding personality to interiors too – Removing EIFS indoors enhances drywall finish options or even unique plaster accent walls.
Rather than accepting ongoing repairs, transforming building exteriors through proper EIFS removal and replacement pays comfort and visual dividends for years.
Proper EIFS Replacement Techniques
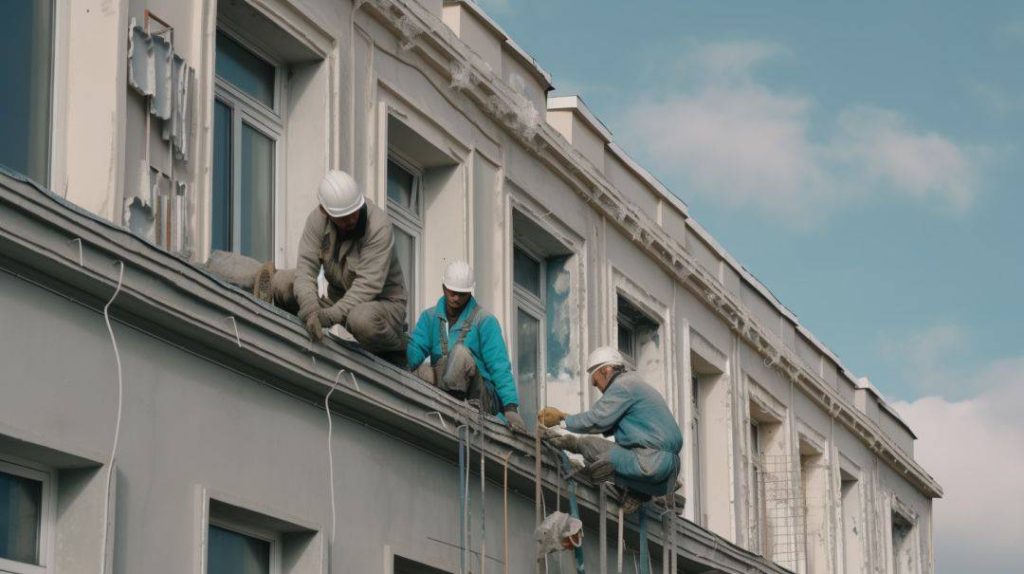
Full Inspection and Removal
The first step with total EIFS replacement is taking the system completely down to the substrate (sheathing, brick, etc) behind it after a thorough inspection reveals all problem areas. This enables:
- Full visibility to gauge necessary repairs
- Rebuilding a new wall system from the ground up
- Integrating updated insulation, barriers, structure
Proper removal is crucial – chiseling, prying, and scraping to avoid damaging the underlying building. Debris then gets fully cleared before rebuilding protective, well-integrated layers in the new facade.
Installation of Water Barriers
Learning from past EIFS woes, the latest building code standards integrate enhanced drainage planes and water barriers to keep structures dry. This involves:
- Tyvek-like moisture repelling membranes
- Vertically installed furring strips to create ventilation/drainage space
- Careful attention to flashing at all openings, transitions
- Durable exterior sheathing less prone to warping/swelling
Hiring Experienced EIFS Replacement Contractors
Trying DIY EIFS removal risks collateral building damage or safety hazards from old adhesives and materials. Indiana Wall Systems leads in full EIFS transformations with over 25 years of experience delivering damage-free building restorations. Their EIFS pros handle:
- OSHA-regulated disposal protocols
- Preserving existing structure and finishes
- Integrating top-quality new cladding systems
- Long workmanship warranties for peace of mind
Benefits of Replacing EIFS
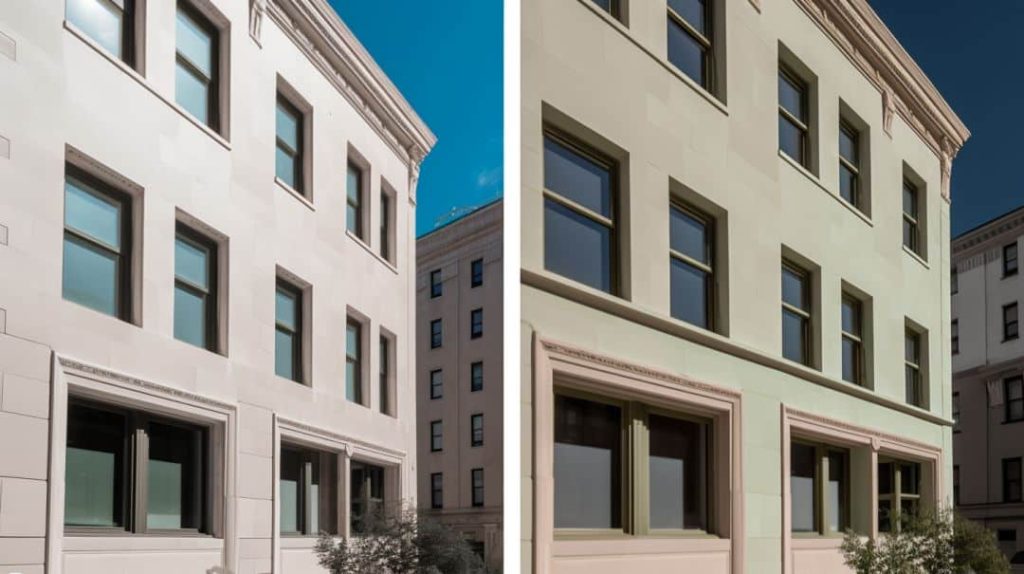
Improved Durability and Weather Resistance
By removing faulty EIFS siding down to the substrate and rebuilding exterior walls using advanced materials and construction methods, homeowners gain exceptionally durable and weather-resistant building enclosures.
Key enhanced durability factors include:
- Multi-layered facade using rigid, resilient materials
- Reinforced scratch, brown, and color finish coats on concrete or masonry
- Copper-infused coatings preventing algae and fungal growth
- Enhanced caulking beads with 50-year flexibility/adhesion capacity
- Termite-resistant insulation/sheathing layers
By utilizing the most cutting-edge components, new facade systems easily outlive early vintage EIFS while standing up to storms, UV rays, pests, and extreme swings in climate.
Low-Maintenance Replacement Options
A major motivator for undergoing EIFS removal is minimizing hands-on upkeep over time compared to high-maintenance coatings with short lifespans.
Superior alternatives like fiber cement and conventional stucco only require:
- Resealing of perimeter caulking every 8-10 years
- Low-pressure power washing debris every 3-5 years
- Potential thin fresh paint coat every 15-20 years
That’s it! No continual worries about cracks reopening, seal failures causing leaks, or premature fading/peels.
Enhanced Visual Appeal
EIFS cladding poses aesthetic challenges with limited color and texture options leading to plain, ambiguous facades. Exciting alternatives enable fully custom aesthetics with unique personality.
Examples of EIFS replacement creativity potential:
- Distressed wood grain fiber cement planks
- Limestone or brick composite accents
- Multi-dimensional shape designs
- Creative paint faux finishes (glazes, metallics, marbling) over cement-based coats
- Enhanced interior wall plastering unrestricted by former barriers
Beauty, dimensional detailing, and welcoming curb appeal all motivate homeowners through the EIFS removal investment.
Conclusion
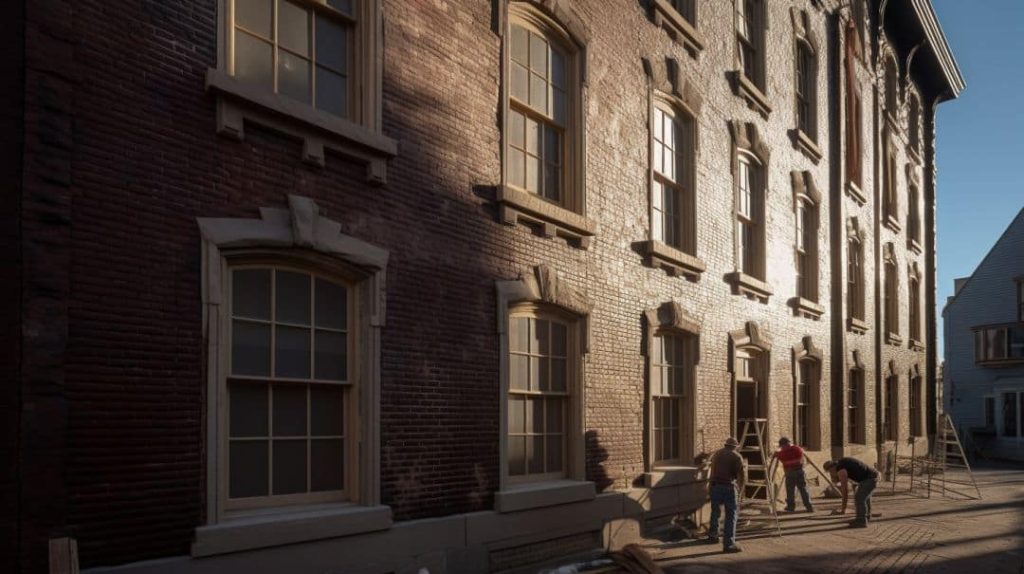
EIFS (Exterior Insulation and Finish Systems) cladding gained favor for its insulation boosts and modern style. However, early formulation vulnerabilities have led homeowners to question persisting with repairs.
As explored, issues like cracking, seal failures, and alarmingly – moisture intrusion – stem from inherent EIFS composition weaknesses. Quality repairs cannot address core gaps or hidden saturation damage.
Yet advanced EIFS materials and methodology improvements offer homeowners hope. Instead of accepting endless repairs, full removal and replacement with new reinforced, integrated EIFS delivers vastly improved longevity and performance.
Key deciding factors on embarking on EIFS replacement include:
- Understanding the full scope of water damage – Inspection often necessitates a complete rebuild
- Desiring durable, low-maintenance EIFS facades – New formulations require far less upkeep
- Seeking improved aesthetics – More finish options help modernize dated plain exteriors
While variable on scope, value payoffs in lifespan, enhancement, and peace of mind make proper EIFS tear-offs and replacements well worth the investment. Contact a reputable local EIFS contractor like Indiana Wall Systems for quotes to transform your home.
FAQs
How long does EIFS last?
EIFS stands for “exterior insulation and finish systems.” Early formulations had lifespan limitations of just 10-20 years before needing repairs. Newer blended EIFS constructions with better integrated water barriers may last 25-30 years with proper maintenance.
What are signs my EIFS needs replacement?
Indicators it’s time to replace instead of spot repairing EIFS siding include extensive cracking, warped foam board areas, chronic sealant failures causing leaks, finishes showing swelling or peeling from moisture issues, and any signs of pests/decay behind façades.
What are the best replacements for damaged EIFS?
Fiber cement planking and conventional 3-layer stucco systems are top alternatives providing superior durability, weather-resistance and design flexibility compared to flawed early EIFS cladding.
How much does full EIFS removal and replacement cost?
Project costs vary based on square footage, custom finishes, necessary sheathing/framing repairs, accessories, the installation company, and local labor rates. However, expect $10-$20 per square foot all-in for tear-off through installing replacement cladding.
How do I maintain or repair EIFS properly?
Always contact experienced EIFS contractors for major repairs instead of DIY patching. But for general upkeep, examine for seal failures annually, re-caulk gaps exceeding 1/16”, power wash gently every 2-3 years, and check for pests/damage behind finishes.