Avoid Costly EIFS Mistakes – Learn How to Spot, Fix, and Prevent Installation Errors to Keep Your Home Safe and Structurally Sound
EIFS problems can turn your dream home into a nightmare with water damage and mold. This exterior wall system needs proper installation to work right and keep your home safe. We’ll show you how to spot common EIFS errors and fix them with expert tips from pros.
Get ready to protect your biggest investment.
Key Takeaways
- EIFS systems need proper installation of all five parts (adhesive, insulation, mesh, base coat, finish) to protect homes from water damage.
- Poor substrate preparation is the top reason EIFS systems fail, causing the material to pull away from walls.
- Face-sealed EIFS systems are now considered defective because they trap moisture with nowhere to drain.
- Water intrusion is the #1 cause of EIFS failures, often leading to mold, rot, and costly structural damage.
- Hiring certified EIFS professionals and following manufacturer guidelines prevents expensive repairs later.
Understanding EIFS (Exterior Insulation and Finish System)
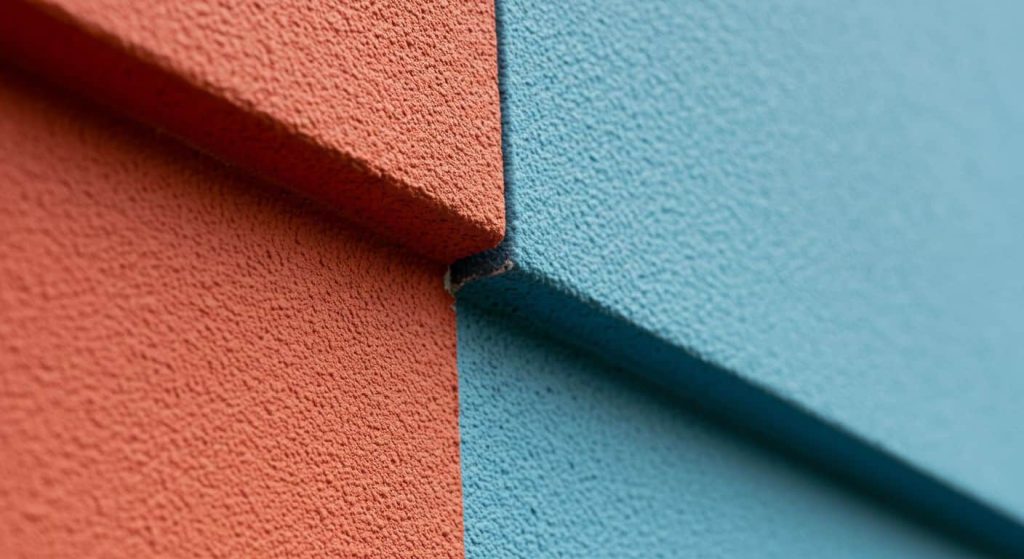
EIFS systems create a modern look while saving energy costs for your home. They use foam boards with special coatings that protect your walls from rain and cold weather.
What is EIFS?
EIFS stands for Exterior Insulation and Finish System. This wall covering looks like stucco but works much better for saving energy. EIFS has five main parts: adhesive, insulation board, mesh, base coat, and finish coat.
The system creates a blanket around your home that keeps heat inside during winter and outside during summer. Many homeowners choose EIFS for its clean look and energy savings.
EIFS first became popular in the 1970s as a way to make buildings more energy-efficient. The system adds a layer of foam insulation to the outside of walls, which helps cut heating and cooling costs.
The outer layers protect your home from rain and wind while giving it a smooth, colored finish. Next, we’ll look at why so many builders and homeowners prefer this system for their properties.
Benefits of EIFS in Construction
EIFS offers homeowners major perks in their building projects. This system combines five key parts – adhesive, insulation board, mesh, base coat, and finish – to create a strong exterior shield.
Homes with proper EIFS enjoy better energy efficiency because the insulation helps keep indoor temps stable. The system also provides excellent weather resistance, protecting your home from rain, wind, and harsh sun.
Accurate EIFS detailing is key to preventing issues during construction and maximizing system performance in the long run.
EIFS gives your home a smooth, attractive look that boosts curb appeal. The finish comes in many colors and textures, letting you match your style perfectly. Unlike some other claddings, EIFS is lighter weight, which can reduce stress on your home’s structure.
With proper installation and regular checks, this system can last for many years while keeping your home cozy and looking great.
Common EIFS Installation Errors
EIFS mistakes can ruin homes and cost a lot to fix. Bad work often comes from rushed jobs, wrong tools, or workers who lack proper training.
Poor Substrate Preparation
Poor substrate prep is the top reason EIFS systems fail. The wall surface must be clean, dry, and flat before any work starts. Dirt, oil, or loose materials can stop the adhesive from sticking right.
Many contractors rush this step, which leads to big problems later. The EIFS can pull away from the wall, letting water get behind it.
Fixing a bad substrate costs much more than doing it right the first time. Face-sealed EIFS systems are known to be defective when the base isn’t ready. Industry standards say you must check the surface and clean it well.
You also need to make sure moisture won’t get trapped. Without proper prep, cracks form and mold grows inside your walls. This can hurt your home’s structure and your family’s health.
Improper Application Techniques
EIFS installers often rush through mixing ratios or apply materials in bad weather. This leads to weak bonds and early system failure. The base coat might be too thin, leaving mesh visible, or too thick, causing cracks later.
Many crews skip vital steps in the five-part system (adhesive, insulation board, mesh, base coat, and finish). Industry standards exist for a reason – skipping them causes big problems! Proper application needs the right tools, correct timing between layers, and careful attention to edges and joints.
Deviations from manufacturer guidelines are the top reason EIFS systems fail, leading to water damage and costly repairs.
Inadequate Waterproofing and Drainage
Poor application methods lead to another major issue: bad waterproofing and drainage. Many EIFS systems fail because water gets trapped behind the surface with nowhere to go. Face-sealed EIFS systems are now seen as defective for this exact reason.
Without proper drainage channels, moisture builds up inside walls, causing mold and rot. The damage often stays hidden until it becomes severe.
Proper moisture control needs both good waterproofing barriers and working drainage paths. Industry standards require weep screeds, flashing, and vapor barriers in all EIFS installations.
Skipping these steps breaks building codes and puts your home at risk. Water intrusion is the #1 cause of EIFS failures, often forcing homeowners to replace entire wall sections at high cost.
Smart drainage solutions include drainage mats, proper sealant around openings, and correctly installed flashing at all joints.
Incorrect Insulation Board Placement
Insulation boards must sit flat against the wall with no gaps between them. Many EIFS problems start when boards aren’t lined up right or have spaces that let water get in. The boards need to be staggered like bricks, not stacked in columns.
Boards with damaged edges or corners should never be used as they create weak spots in your home’s defense system.
Fixing poorly placed boards often means taking off the whole EIFS system and starting over. This costs much more than doing it right the first time. Industry standards require boards to be butted tightly together, with joints offset at least 6 inches.
Proper board placement forms the backbone of your EIFS system’s ability to keep moisture out and maintain thermal insulation. Let’s now look at how these installation errors can lead to serious problems for homeowners.
Insufficient Expansion Joints
Expansion joints are vital parts of your EIFS system that allow the walls to move as temps change. Many homes have problems because these joints are missing or not placed right. Your EIFS needs these gaps to expand and contract without cracking.
The lack of proper joints leads to stress on the surface, which causes cracks and opens paths for water to get in.
EIFS experts know that adding the right number of joints at the right spots stops big problems later. Industry standards call for joints every 75 feet and at floor lines, roof connections, and where different materials meet.
Face-sealed EIFS without good joints often fails and may need full replacement. This mistake costs homeowners thousands in repairs that might not be covered by insurance.
Problems Caused by EIFS Installation Errors
Bad EIFS jobs can lead to big problems for your home. Moisture can get trapped behind the walls, causing mold, rot, and damage that costs thousands to fix.
Moisture Intrusion and Mold Growth
Poor EIFS setup creates big problems for homes. Water gets trapped behind the system with nowhere to go. This happens most often with face-sealed EIFS, which experts now call “defective” as exterior cladding.
The trapped moisture leads to mold that grows fast in dark, wet spots. Your walls can rot from the inside out without you seeing it until major damage occurs.
Mold doesn’t just hurt your house – it can make your family sick too. The water damage weakens your home’s frame and can cost thousands to fix. Many insurance plans won’t even cover EIFS water damage! Regular checks by an EIFS inspector can catch these issues early.
Looking for dark spots, musty smells, or peeling finish helps spot trouble before it spreads through your walls and harms your home’s structure.
Cracking and Structural Damage
EIFS problems often start with small cracks that grow bigger over time. These cracks let water seep behind the surface, causing wood rot and damage to your home’s frame. Face-sealed EIFS systems are known to be flawed by design and can’t protect your walls properly.
Industry experts warn that cracks in EIFS can hide major structural issues that may cost thousands to fix. Water trapped behind cracked EIFS creates the perfect spot for mold and decay, which weakens your home’s support system.
Fixing these issues isn’t as simple as patching cracks. Many homes with damaged EIFS need complete removal and replacement of the entire system. The five parts of an EIFS wall – adhesive, insulation board, mesh, base coat, and finish – must all work together to prevent damage.
If one part fails due to poor setup or low-quality materials, the whole wall is at risk. Next, we’ll look at common mistakes people make when trying to repair EIFS problems.
Reduced Energy Efficiency
Faulty EIFS installation often leads to poor energy performance in your home. Gaps between insulation boards let heat escape in winter and enter during summer. This happens because EIFS works as a thermal barrier only when all five components – adhesive, insulation board, mesh, base coat, and finish – are installed correctly.
Industry studies show that even small installation errors can cut your insulation value by up to 40%.
Improper drainage and moisture buildup make things worse for your energy bills. Wet insulation loses its ability to block heat transfer. The original R-value drops significantly, forcing your heating and cooling systems to work harder.
Fixing these issues requires more than simple patches – you might need complete sections redone by certified EIFS professionals who follow manufacturer guidelines exactly.
Aesthetic Issues
Poorly installed EIFS systems create ugly problems that hurt your home’s curb appeal. Uneven surfaces, color mismatches, and visible seams make your exterior look shabby. Cracks in the finish coat let dirt collect and create dark streaks down your walls.
These flaws don’t just look bad – they signal deeper problems with your EIFS system. The five key components (adhesive, insulation board, mesh, base coat, and finish) must work together perfectly for a smooth, attractive result.
Fixing these eyesores often requires more than simple patching. Surface stains might point to water damage behind your walls. Bulges or ripples in the surface show that the insulation boards weren’t placed correctly.
Many homeowners face these issues because installers didn’t follow the manufacturer’s guidelines. Expert repair services can fix these problems and restore your home’s beauty. Let’s explore the common mistakes people make when trying to repair EIFS problems.
Top EIFS Repair Mistakes and How to Avoid Them
EIFS repairs need careful work to fix problems right the first time. Many homeowners face costly fixes because of these common repair mistakes.
- Skipping proper surface prep – Dirt, loose material, and old sealant must be removed before repairs start. Clean surfaces help new materials stick better and last longer.
- Using wrong materials – Each EIFS system needs specific products made to work together. Mixing brands or using cheap alternatives leads to cracking, peeling, and water damage.
- Ignoring water damage signs – Water stains, mold, or soft spots mean moisture has gotten in. Fixing just the surface without finding and stopping the leak source wastes money and time.
- Patching without fixing drainage – Face-sealed EIFS systems often fail because they trap water. Adding proper drainage paths during repairs stops future moisture problems.
- DIY repairs without training – EIFS needs special skills to fix right. Homeowners who try to patch their own walls often make things worse and face bigger bills later.
- Missing expansion joints – EIFS needs room to move with temperature changes. Leaving out joints during repairs causes cracks as the building shifts.
- Poor flashing installation – Water gets in where walls meet windows, doors, and roofs. Correct flashing keeps water out of these spots.
- Not checking the whole system – One crack often means other problems exist. Complete inspections find all issues before they grow worse.
- Rushing the repair process – Each layer of an EIFS repair needs time to set before the next step. Hurrying causes weak spots and early failure.
- Hiring unqualified contractors – Many repair companies lack proper EIFS training. Ask for proof of certification and past work before hiring anyone.
Expert Solutions for Correcting EIFS Installation Errors
Fixing EIFS errors takes skill and the right methods. Expert solutions can save your home from water damage and costly repairs.
Ensuring Proper Substrate Preparation
Good substrate prep is the backbone of any EIFS system. Before adding any materials, check your wall surface for cracks, dirt, and moisture. Clean it well and fix all damage. The wall must be flat and dry for the EIFS to stick right.
Many EIFS problems start with poor surface prep, which leads to water getting in later. Industry experts point out that skipping this step causes most EIFS failures in homes.
Proper prep means using the right tools and methods based on what your wall is made of. Wood, concrete, and brick all need different prep work. You need to apply the right primer and make sure the surface can bond with the adhesive.
Face-sealed EIFS systems often fail because installers rush through this key step. Taking time now saves you from costly repairs and water damage later.
Using High-Quality Materials
Top-grade materials make all the difference in EIFS projects. Face-sealed systems often fail because of poor-quality components that break down over time. The right adhesives, mesh, base coat, and finish create a strong barrier against water and weather damage.
Many EIFS failures trace back to cheap materials that can’t stand up to rain or temperature changes.
Your home needs protection from moisture – the number one enemy of EIFS systems. Quality materials cost more upfront but save money by avoiding costly repairs later. EIFS manufacturers provide specific guidelines for which products work best together.
Using these approved materials helps your system last longer and perform better against severe weather. Cutting corners on materials leads to cracking, water infiltration, and reduced durability of your home’s exterior envelope.
Adhering to Manufacturer Guidelines
EIFS makers create clear rules for a reason – they work! Each brand has tested their products and knows exactly how they should be used. The five parts of an EIFS system (adhesive, insulation board, mesh, base coat, and finish) must be installed in the right order with proper methods.
Many EIFS problems start when workers skip steps or change the process. Studies show that face-sealed EIFS systems are often called “defective” because people don’t follow the maker’s rules.
Your home deserves better than that!
Following the product guides helps your EIFS last longer and work better. The guides tell you how thick each layer should be, how long to wait between steps, and what tools to use.
They also explain how to handle corners, joints, and spots where pipes or wires go through the wall. Smart homeowners keep copies of these guides and make sure their workers read them too.
This simple step can save you from costly repairs later on. The EIFS industry has strict standards because they know what happens when people take shortcuts.
Implementing Effective Waterproofing Systems
Following manufacturer rules is just the start. Good waterproofing makes or breaks your EIFS system. Water is the top enemy of any stucco system, causing mold and rot that hurt your home’s structure.
A proper drainage system must include water-resistant barriers, flashing around windows and doors, and weep screeds at the bottom. These parts work together to push water away from your walls.
Many EIFS problems come from skipping these steps during installation. The right waterproofing setup costs less than fixing water damage later. Smart homeowners make sure their EIFS installer uses high-quality materials and follows industry standards for moisture control.
Correcting Insulation Board Alignment
After setting up proper waterproofing, fixing insulation board alignment is the next vital step. Crooked or poorly placed boards create weak spots in your EIFS system. These gaps let water sneak in and cause mold or rot.
The five parts of an EIFS system must work together – adhesive, insulation board, mesh, base coat, and finish. Each part matters for your home’s safety.
Fixing board alignment means checking that each panel sits flush with others. Gaps must be filled with proper materials, not just caulk or foam. Many EIFS failures happen because boards weren’t put on right.
Face-sealed EIFS systems are now seen as flawed and unsafe for homes. Good board placement stops cracks, keeps energy bills down, and makes your walls look smooth. Always hire pros who follow the maker’s rules for best results.
EIFS Expert Tips for Flawless Installation
Getting EIFS right the first time saves you money and stress. These expert tips will help you spot good work and talk to your contractor about proper installation.
- Check for proper surface prep before work starts. Clean walls must be free of dust, dirt, and old paint that could stop the system from sticking.
- Make sure installers use the exact materials listed by the EIFS maker. Mixing products from different brands can lead to system failure and void warranties.
- Watch for correct mesh placement in the base coat. The mesh gives strength to the system and must cover all areas with proper overlap at seams.
- Insist on proper drainage systems behind the EIFS. Water needs a way to escape if it gets behind the finish to prevent mold and rot.
- Look for neat, even joints between insulation boards. Gaps or misaligned boards can cause cracks in your finish later.
- Ask about expansion joints in your EIFS system. These spaces let the wall move slightly without cracking during weather changes.
- Make sure all wall openings have proper flashing and sealant. Windows, doors, and other spots need extra care to stop water leaks.
- Request that installers follow the right order of steps. Rushing or skipping steps leads to big problems later.
- Hire only certified EIFS pros with proof of training. Face-sealed EIFS systems are known to be flawed, so make sure your team knows modern methods.
- Plan for at least two coats of finish for the best look and protection. A single coat may not give enough cover or durability.
- Ask about the right thickness for your insulation boards. Too thin won’t save energy, too thick might cause other issues.
- Get a clear maintenance plan in writing. Regular checks can catch small problems before they become big repairs.
Preventing EIFS Installation Errors
Preventing EIFS installation errors starts with proper planning and expert help. Smart homeowners hire certified EIFS pros who know how to follow building codes and avoid costly mistakes.
Pre-Installation Inspections and Planning
Good planning stops EIFS problems before they start. Check your home’s surface for cracks, rot, or damage first. These issues must be fixed before any EIFS work begins. Make sure the surface is clean and dry too.
Moisture tests help find hidden water that could harm your new system later. A proper plan includes checking that all materials match the maker’s rules. Face-sealed EIFS systems often fail, so pick a drainage-type system instead.
Smart planning means getting the right pros who know industry standards. They should map out where water might get in and plan proper seals. This step is not just nice—it’s needed to keep your home safe and dry.
Hiring Certified EIFS Professionals
After planning your EIFS project, finding the right people to do the work is key. Certified EIFS pros have special training in the five main parts of the system: adhesive, insulation board, mesh, base coat, and finish.
They know how to follow maker rules and avoid the mistakes that lead to water damage. Many home problems start with poor installation that lets moisture in, causing mold and rot.
Picking a certified expert costs more upfront but saves money later. These pros stay up-to-date on industry standards and know how to install drainage systems that keep water out. Face-sealed EIFS systems are now seen as flawed, so you need someone who can install modern, better systems.
Good installers will check your home first, use quality materials, and make sure all parts work together to protect your walls.
Regular Training for Installers
EIFS installers need ongoing training to stay up-to-date with best practices. Many EIFS problems stem from workers who don’t know the right steps. Training helps crews learn proper surface prep, mesh placement, and moisture control methods.
Good training programs focus on the five key EIFS parts: adhesive, insulation board, mesh, base coat, and finish layer.
Training must cover how to follow maker guidelines exactly. Face-sealed EIFS systems have been called “defective” when not installed right. Smart homeowners ask if their EIFS crew gets regular training on new tools and methods.
This simple step can prevent costly damage and repairs down the road. Trained workers spot issues early and fix small problems before they become big ones.
Compliance with Building Codes and Regulations
Training your installers is just the first step. Local building codes must be followed for all EIFS work. These rules exist to keep homes safe and strong. Each area has its own rules about how thick the insulation should be, what materials you can use, and how to install drainage systems.
Breaking these rules can lead to fines, failed inspections, and unsafe homes. Smart homeowners check that their EIFS contractor knows all local codes before starting work. Face-sealed EIFS systems are now seen as flawed in many areas and may not meet current standards.
Your local building department can tell you what rules apply to your home. They might require special permits or inspections for EIFS work. Many insurance companies won’t cover damage from poorly installed EIFS, so doing it right matters.
The right EIFS system needs five key parts: adhesive, insulation board, mesh, base coat, and finish coat. Each part must meet local fire safety rules too. Getting all this right means your EIFS will look good, work well, and pass all needed inspections.
Repairing Damaged EIFS Systems
Damaged EIFS systems need fast action to stop more harm. Our repair team fixes cracks, patches holes, and adds new drainage to keep water out.
Addressing Mechanical Damage
EIFS systems can suffer damage from impacts, scrapes, or punctures. These issues need quick fixes to stop water from getting inside your walls. First, clean the damaged area with a soft brush.
Then apply a matching base coat to fill in holes or cracks. Make sure to embed new reinforcement mesh if the old mesh was torn. For bigger damage spots, you might need to cut out and replace sections of the insulation board.
Using the right tools and materials is key – always match the original EIFS components for the best results. Proper repair prevents moisture problems that could lead to mold or rot in your home’s structure.
The next step after fixing mechanical damage is upgrading your drainage systems to prevent future moisture issues.
Fixing Cracks and Impact Damage
After fixing mechanical damage, you’ll need to address cracks and impact issues in your EIFS system. Small cracks often start from improper installation or normal house settling. Fix these right away to stop moisture from getting in.
For hairline cracks, apply a matching sealant after cleaning the area with a soft brush. Larger cracks need special care – cut out the damaged section and patch it with fresh base coat and mesh before adding new finish.
Impact damage from hail, toys, or lawn equipment needs quick repair too. The five-part EIFS system (adhesive, insulation board, mesh, base coat, and finish) must be fixed layer by layer.
Clean the damaged spot, cut away loose materials, and rebuild each layer according to the maker’s rules. This careful repair stops water problems and keeps your home looking good. Face-sealed EIFS systems need extra care since they’re more likely to have issues if not fixed right.
Replacing Defective Components
Beyond fixing cracks, you might need to replace parts of your EIFS system that can’t be repaired. Damaged insulation boards, rusted mesh, or worn-out base coats must go. Industry experts agree that face-sealed EIFS systems are often not fit for use as exterior cladding.
This means you may need to replace more than just small sections.
The five main parts of an EIFS system include adhesive, insulation board, mesh, base coat, and finish. Each part must work together. If one fails, the whole system suffers. Deviations from standard guidelines during the first install often lead to big problems later.
For best results, hire pros who know how to match new parts with your existing system. They’ll make sure new pieces bond well and keep water out of your walls.
Upgrading Drainage Systems
After replacing broken parts, your EIFS system needs proper water control. Old drainage systems often fail to keep moisture away from walls. Modern EIFS drainage systems use special channels and weep screeds that let water escape.
These upgrades stop water from getting trapped behind the finish layer.
Many homeowners don’t know that face-sealed EIFS systems are now seen as defective for exterior walls. Adding drainage paths can fix this major flaw. New systems include air barriers and water-resistant backings that work together.
This upgrade costs less than full recladding and helps prevent mold growth. Good drainage also extends the life of your stucco finish and keeps your home’s structural parts safe from rot.
Advanced Techniques and Tools for EIFS Installation
Modern EIFS pros now use high-tech tools and better materials to get top results – from smart adhesives to new drainage systems that stop water damage before it starts.
Use of Modern Adhesives and Coatings
Today’s EIFS products offer better sticking power and weather defense than older versions. New glues bond insulation boards firmly to walls, cutting the risk of panels coming loose.
These products help stop water from getting in – a big plus since moisture causes most EIFS damage. Many new coatings also fight mold growth and stand up to harsh weather.
Picking the right products matters for your home’s EIFS system. The best adhesives work with all five parts of an EIFS wall: the glue, insulation board, mesh, base coat, and finish layer.
Quality coatings boost your facade’s life span and keep it looking fresh. For best results, make sure your contractor uses only items that meet strict industry rules and the maker’s guides.
Incorporating Vapor Barriers and Weep Screeds
Vapor barriers and weep screeds play key roles in keeping your EIFS system dry and damage-free. Vapor barriers stop moisture from getting trapped inside walls, which helps prevent mold growth and rot.
They form a crucial layer in the EIFS system’s five components. Proper placement of these barriers follows strict industry standards to avoid installation errors that lead to costly repairs.
Weep screeds create drainage paths for any water that might get behind the EIFS cladding. These metal strips sit at the bottom of walls and let water escape instead of soaking into your home’s structure.
Many EIFS problems stem from missing or poorly installed weep screeds. Face-sealed EIFS systems without these drainage features often fail and may need complete replacement.
Innovations in EIFS Detailing and Finishing
New tools have changed how pros detail and finish EIFS systems. Digital scanners now find moisture spots before they cause damage. Smart coatings resist dirt and need less cleaning.
These coatings also block UV rays that can fade colors over time. Many new finish options match brick, stone, or wood – giving homes a custom look without the high cost.
Improved sealants create better bonds at joints and edges where water often gets in. The latest mesh products add strength to the base coat, making walls more impact-proof. These upgrades help avoid the common issues that make insurers exclude EIFS from coverage.
For homeowners, these new products mean less repair work and longer-lasting walls that keep their beauty year after year.
Importance of Maintenance and Inspections
Regular checks of your EIFS system can spot small issues before they turn into big problems. A simple yearly inspection by a pro can save you thousands in repairs and extend the life of your exterior finish.
Routine Inspections to Identify Issues Early
Checking your EIFS system often helps catch small problems before they grow. Look for cracks, water stains, or spots where the finish looks different. These signs point to moisture issues that can harm your home’s structure.
Industry experts say most EIFS damage starts with tiny flaws that go unnoticed for months. A quick walk around your house every season can save you thousands in repair costs.
Your home needs special care at joints, windows, and where pipes come through the walls. These spots let water in if not sealed right. Face-sealed EIFS systems are known to fail because they trap moisture inside walls.
Smart homeowners take photos during each check to track changes over time. Next, we’ll explore how to keep your EIFS surfaces clean and well-maintained for lasting beauty.
Cleaning and Maintaining EIFS Surfaces
After finding issues early through routine checks, proper cleaning of your EIFS surfaces becomes the next vital step. Dirt and grime can hide small cracks where water might get in.
You should wash EIFS walls with mild soap and water using a soft brush or low-pressure spray. Harsh cleaners or power washers can damage the finish coat and create new problems. Most EIFS makers suggest cleaning at least once a year to keep the surface looking fresh.
Regular care stops small issues from growing into big repairs. Apply new sealant around windows and doors as needed since these spots often let moisture in. Check for any stains that might show water problems.
Touch up damaged areas with matching finish materials right away. This simple upkeep saves money and extends your EIFS system’s life. The quality of your maintenance directly affects how long your exterior walls will last and how well they protect your home.
Long-Term Care for System Longevity
Your EIFS needs regular care to last many years. Experts say you should check your walls twice a year for cracks, stains, or damage. Clean your EIFS surfaces with mild soap and water to remove dirt that could trap moisture.
Never use power washers as they can harm the finish coat. Touch up small cracks right away with proper sealants made for EIFS systems.
Moisture is the biggest enemy of EIFS walls. Make sure all joints around windows, doors, and other spots stay sealed tight. Replace worn sealants before they fail. Face-sealed EIFS systems need extra care since they lack proper drainage.
Many home insurers won’t cover damage from these older systems. A yearly check by a trained EIFS expert costs less than fixing major water damage later.
Conclusion
Fixing EIFS errors needs care and skill. Good repairs protect your home from water damage and keep it looking nice. Finding a certified EIFS expert saves money in the long run by fixing problems right the first time.
Regular checks of your EIFS system catch small issues before they grow into big, costly ones. With proper fixes and upkeep, your EIFS can last for many years while keeping your home energy-efficient and beautiful.
FAQs
What are common EIFS stucco problems?
Properties with EIFS have frequent reports of moisture penetration, which can compromise the structural integrity of buildings. Poor adhesion, cracking, and water intrusion are also common issues that need expert stucco repair.
How can I prevent moisture damage in my EIFS system?
Regular inspections to identify potential sources of water intrusion are key. Proper installation and maintenance of sealants around windows and doors will help prevent moisture from getting trapped behind the synthetic stucco.
Why do insurers exclude coverage for EIFS damage?
Many insurance companies view EIFS as a high-risk exterior due to its unique risks associated with moisture problems. The quality of installation plays a big role in whether they’ll cover damages.
What should I look for during EIFS inspections?
Check for stucco cracks, signs of water damage, and areas where the system might be pulling away from the building. Look at places where different materials meet, as these are common spots for sealant failure.
Can existing EIFS be fixed or should it be replaced?
Existing EIFS can often be repaired through proper remediation techniques like sealant application and surface preparation. The decision depends on the extent of damage and whether design flaws exist in the current system.
What makes expert EIFS repair different from DIY fixes?
Expert stucco repair involves tailored solutions that address both visible damage and hidden problems. Professionals understand the specific EIFS installation methods needed for your climate and can provide peace of mind that DIY approaches simply can’t match.